ORIGINAL ARTICLE
FIGUEROA, Yusleidi Cuesta [1], LABRADA, Víctor Mir [2], HERNÁNDEZ, Yusdel Díaz [3], FIGUEREDO, Marcos Batista [4], NÉRI, Thais de Souza [5], SILVA, Alexandre do Nascimento [6], FONTOURA, José Roberto de Araújo [7], MONTEIRO, Roberto Luiz Souza [8]
FIGUEROA, Yusleidi Cuesta et al. Proposed maintenance program for the 1k62 lathe: improved cycles and availability. Revista Científica Multidisciplinar Núcleo do Conhecimento. Year. 10, Ed. 01, Vol. 02, pp. 146-162. January 2025. ISSN: 2448-0959, Access link: https://www.nucleodoconhecimento.com.br/mechanical-engineering/proposed-maintenance-program, DOI: 10.32749/nucleodoconhecimento.com.br/mechanical-engineering/proposed-maintenance-program
ABSTRACT
Maintenance of machine tools is key to guaranteeing their efficiency, prolonging their useful life and maintaining quality in manufacturing processes. The present work referred to the study of the 1k62 parallel lathe located in the Faculty of Mechanical Engineering, which is in the Technological University of Havana. The main objective was to design a maintenance program, identify the necessary resources for its implementation and calculate the availability of the equipment. A new maintenance cycle was evaluated and proposed to ensure the availability of the equipment and extend its useful life. Finally, it was suggested to continuously review and adapt the program based on operating conditions and feedback from technical staff to ensure its long-term effectiveness. This proposal supports research in the framework of higher education in the faculty of Mechanical Engineering.
Keywords: Preventive maintenance, Parallel lathe 1K62, Availability, Resource management.
1. INTRODUCTION
According to Márquez et al. (2008), maintenance is the combination of all technical and management measures during an item’s life cycle to maintain or restore it to a state where it can fulfill a required function. Maintenance, as defined in previous research, involves technical and management activities aimed at maintaining or restoring the condition of a company’s equipment through repair, replacement, or modification based on the company’s conditions.
In traditional maintenance approaches, the requirements for each component were determined according to its actual or assumed technical characteristics, without considering the consequences of failure. These timelines were applied uniformly across similar objects, ignoring the different consequences arising from various operational contexts (Stuchlý et al.; 2018).
Michael et al. (2022) highlights the increasing importance of maintenance, as the reliability of production systems is a key factor for competitiveness. He states, “maintenance is the combination of all the technical and administrative measures that serve to maintain or restore the planned functional state.” He explains that today, maintenance, inspection, and repair of machines and installations are carried out reactively due to faults or according to the manufacturer’s instructions.
Díaz et al. (2017) propose another criterion, stating, “Currently, maintenance development is focused, among other directives, on reducing costs, increasing availability and operational reliability, optimizing performance, and extending the useful life of assets.”
To develop a maintenance plan, it is essential to understand the different types of maintenance. Sosa et al. (2018) identify the types of maintenance as corrective, preventive, predictive, and proactive, focusing on carrying out planned or unplanned actions to prevent failures that could cause irreparable damage to the equipment.
Costa et al. (2023) define preventive maintenance as a pre-established intervention process at defined time intervals aimed at reducing or avoiding failures or machine downtime that affects performance. Preventive maintenance planning, known as systematic prevention, is based on specific time intervals that define machine stops.
Marrero et al. (2022) highlight that the programming and planning processes of maintenance are the basis for the sustainability of the production process, enabling assets to be serviced throughout their life cycle. These processes depend entirely on time and the asset’s operation. In the manufacturing industry, increasing productivity and product quality are constant goals. The condition of machine tools directly impacts the production rate and quality of machined parts (Thoppil et al.;2020)
Recent studies emphasize the need for critical analysis of mechanical systems to support maintenance decision-making, pointing out the lack of robust methodologies for maintenance prioritization in the industry (Crespo et al.; 2016).
Abdelrahim and Vizvári (2017) underscore the importance of identifying critical machine components and potential failure modes in predictive maintenance and Remaining Useful Life (RUL) prediction. The industrial sector has long implemented various methodologies for reliability and failure analysis of machine tools. Preventive maintenance allows us to identify potential failures before they occur and address them proactively. This requires resources, including materials, spare parts, operators or maintenance specialists, subcontracted labor services, or rental of specialized equipment, often referred to as planning.
Another critical factor is equipment availability. Machine Tool (MT) availability is essential for production scheduling. The availability of machine tools depends on their reliability (Meaning Between Failures, MTBF) and maintainability (Mean Time To Repair, MTTR), both influenced by multiple factors and uncertainties (Gunjan et al.; 2023).
Patil et al. (2021) analyzes the reliability, maintainability, and availability of Computer Numerical Control Machine Tools (CNCMT), highlighting their importance in mass production industries. They propose a generalized framework for analyzing Time Between Failures (TBF) and Time To Repair (TTR) data, integrating these with Markov chains.
Jain and Kumar (2021) focus on predicting the available capacity of a non-Markovian model for complex multi-component repairable manufacturing systems. They conclude that improving the availability and reliability of complex manufacturing systems requires a thorough understanding of the causes and mechanisms of failures and emphasize effective inspection and repair strategies.
Sevindik (2006) developed an exact branching and binding procedure along with three specific heuristic algorithms to address the total time of completion problem. He concludes that programming with machine availability constraints is complex and that developing effective algorithms is crucial for managing these challenges.
In the Mechanical Workshop at the Faculty of Mechanical Engineering, Technological University of Havana, various machine tools are utilized, including the 1K62 lathe. Despite its age, the lathe does not exhibit wear that would compromise the shape and position requirements of the parts produced. This is due to its use in research validations and technology checks, rather than in mass production like in a factory. However, the lathe currently lacks a maintenance plan, which is crucial to ensure its quality and the durability of its components.
2. MATERIALS AND METHODS
2.1 ANALYSIS METHODOLOGY
To ensure the equipment’s availability, the following development plan is proposed:
- Select the equipment: parallel lathe machine tool.
- Identify the parts that make up the study team.
- Identify the managers and technicians involved in maintenance actions.
2.2 EQUIPMENT SELECTION: PARALLEL LATHE TYPE MACHINE TOOL. IDENTIFICATION OF PARTS THAT MAKE UP THE STUDY TEAM
The machine tool under study is the 1K62 parallel threading and rolling lathe. Figure 1 shows a sketch of the equipment with its main parts described below:
- Fixed Head: Inside is the gearbox with cogwheels and shafts attached. The main spindle is also located here, to which various plates or devices are attached to hold the semi-product.
- Interchangeable Wheel Guitar
- Advance Box: Contains toothed wheels that ensure different speed values for both common machining and thread processing.
- Supports: Referred to as legs by the manufacturer; the main engine is on the left and the coolant reservoir is on the right.
- Apron: Contains the mechanism to connect and disconnect the spindle drive, its reversal, and controls for manual control.
- Longitudinal Carriage: Houses the apron, transverse carriage, steerable carriage, tool turret, parts of the cooling duct, and lighting.
- Bed: The lathe’s base, where the fixed head, moving head, and longitudinal carriage are attached and slid along the guides; the motor for the fast gear is inside on the right side.
- Moving Head: Located on the far right, opposite the fixed head, it slides along the lathe bed guides.
Fig.1: Front view of the lathe (1K62) with its main parts marked
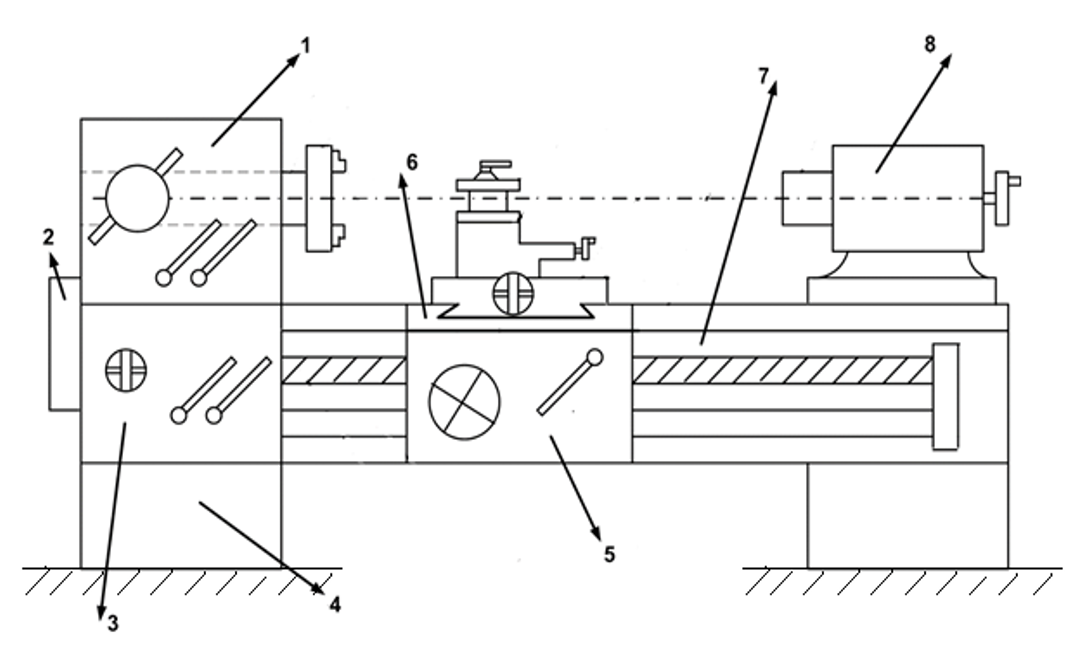
The workshop lacks a maintenance program and material resources. The machine tools have not undergone any systematic revisions or repairs since the year 2000. Figure 2 illustrates the defects detected from the collected information and the materials used for repairs. A survey of the historical records on the lathe was conducted, detailing the different types of maintenance work carried out on the equipment over the years. This information is also presented in Figure 2.
Fig. 2: Historical behavior of the facts collected by information
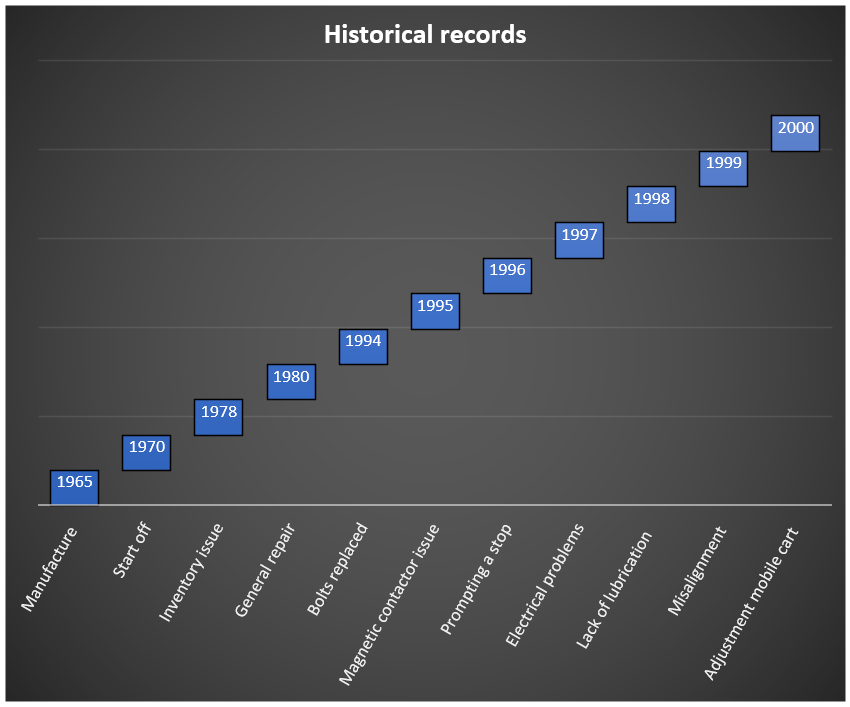
For the maintenance plan proposal of the 1K62 lathe, the 11 steps described by Costa et al. (2023) were considered. These steps for planning preventive maintenance in gear lathes include title of the plan, group of machines, periodicity, type of day, evaluation date, maintenance equipment, maintenance planner, consumables, specialties, protective equipment, and support tools and equipment.
2.3 REPAIR CYCLE STRUCTURE AND DURATION
The repair cycle is the time the equipment operates between two general repairs. The operations in the cycle include revision (R), small repair (P), medium repair (M), and general repair (G). The 1k62 lathe weighs 2401 kg, equivalent to 2.4 tons, classifying it as a light machine tool. Figure 3 illustrates the cycle, where (t0) represents the time between operations, (tr) the time between repairs, and T the duration of the cycle, which is the total hours the equipment must work between two general repairs. This time is calculated as shown in equation 1.
Fig. 3: 1K62 lathe repair cycle
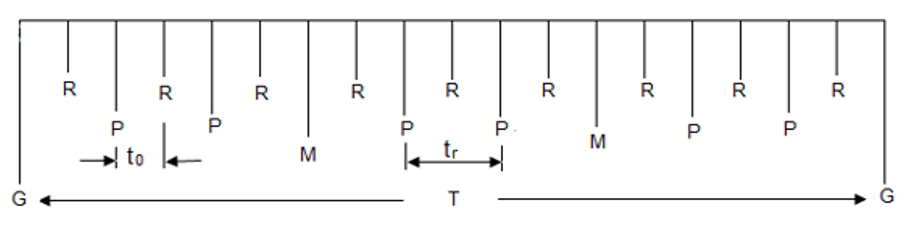
Where:
N: coefficient that relates to the type of production.
M: coefficient that relates to the type of production.
Y: coefficient that relates to the environmental conditions where the equipment is located.
Z: coefficient that relates to the weight of the equipment.
K: Theoretical duration of the cycle.
2.4 CALCULATION OF THE TIME BETWEEN OPERATIONS AND BETWEEN REPAIRS
After selecting the corresponding structure of the repair cycle and calculating the duration of the repair cycle in hours, the time between operations and the time between repairs can be determined using equations 2 and 3.
According to [16], to obtain the coefficients, the objective of the asset is considered. The most used materials are alloys of cast aluminum, cast iron, steel 45, and austenitic and ferritic stainless steel. The type of production is individual, and the working environment includes dust and humidity without the use of corrosive materials. The weight of the equipment also plays a role. These factors influence the theoretical duration of the cycle, which considers the machine’s weight, years of operation, and whether they exceed 20 years. In this case, the study asset.
2.5 DEGREE OF COMPLEXITY AND RULES FOR REPAIR
The volume and complexity of repair work depend on the machine’s complexity and the type of repair. To plan the repair of the 1K62 lathe, it is essential to understand its degree of complexity. This degree helps schedule the appropriate amount of work for a specific piece of equipment and provides an index of the repair’s complexity. The lathe’s complexity is divided into two parts: mechanical (M) and electrical (E), as shown in Tables 1 and 2.
Table 1. Degrees of complexity of the 1K62 lathe.
Model | Center height (mm) | Center spacing (mm) | Complexity | |
Mechanics | Electric | |||
1K62 | 200 | 710 | 11 | 8.5 |
Source: Authors (2024).
Table 2. The number of hours needed for a degree of complexity.
PPM Periodic Work Type | Number of hours needed by degree of complexity | ||
Adjustment and assembly | Machining | Total | |
Revision | 1.0 | 0.5 | 1.5 |
Small repair | 5.0 | 3.0 | 8.0 |
Medium repair | 22.0 | 10.0 | 32.0 |
General repair | 42.0 | 18.0 | 60.0 |
Source: Authors (2024).
2.6 ESTIMATE OF EQUIPMENT AVAILABILITY
Availability is the ratio between the difference in the total hours considered (HCAL) and the number of hours of maintenance intervention (HRMN) for each item observed, relative to the total hours in the period considered. Equation 4 is used to calculate availability.
Availability is the relationship between the difference in the number of hours in the period considered (total hours, (HCAL) with the number of hours of intervention by maintenance personnel (HRMN) for each item observed and the total number of hours in the period considered. Equation 4 is used to calculate availability.
The availability of an item represents the percentage of time it takes for the operating body to perform its activities. This is calculated using equation 5.
Where:
: It is the sum of all the times of each maintenance job, including mechanical and electrical, these also calculated above.
3. RESULTS AND DISCUSSION
The study asset has an operating time of 54 years, with a theoretical lifetime value of K = 23400. Using the coefficients N = 1.5, M = 0.75, Y = 0.8, and Z = 1, and substituting these values in equation 1, the cycle time is calculated, resulting in a value of T = 21060 hours, since the production of the asset is unitary, and each part has different characteristics. The data for the calculation of the repair cycle time are maintained, except for the data relating to the type of production (N), therefore, we have N = 2, M = 0.75, Y = 0.8, Z = 1, K = 23400. Substituting again the values of these coefficients in equation 1, the new cycle time is obtained, giving as a result T = 28 080 hours.
Due to the above conditions under which the lathe operates, the structure of the repair cycle was expanded. With the values of the time between operations, the time between repairs, the hours of each Planned Preventive Maintenance (PPM) job and the cycle time, the repair cycle can be illustrated as shown in figure. 4. Substituting the new values of R=8, P=6 and M=1 into equations 2 and 3 gives the time between operations as 1755 hours, and the time between repairs as 3510 hours.
Fig. 4: Updated maintenance cycle for the 1k62 lathe
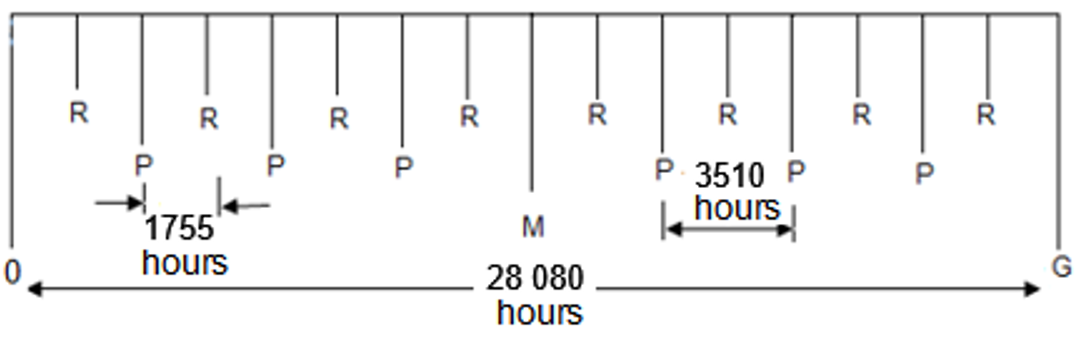
3.1 DEGREE OF COMPLEXITY AND REPAIR RULES
The degree of complexity is defined according to the operations to be performed on the equipment (Table 3). For real exploitation conditions, a calculation base is established that considers the man-hours worked over a year, equivalent to 11 months. Under these conditions, calculations are made according to the labor legislation of the case study, resulting in a time fund of 2112 hours per year.
Table 3: Operations to be carried out
Operation | Mechanics (man-hours) | Electric (man-hours) |
Revision | 11 | 8.5 |
Small repair | 55 | 42.5 |
Medium repair | 244 | 187 |
General repair | 462 | 357 |
Total | 772 | 595 |
Number of people | 1 | 1 |
Source: Authors (2024).
3.2 EQUIPMENT AVAILABILITY
To estimate the values of the proposed maintenance plan, the date the lathe was put into operation, the legally established working day, and other organizational aspects are taken as references. By applying the data in equations (1-5), it is determined that the equipment’s availability for operations is 90%, leaving a time reserve for the maintenance cycle of Hcal equal to 23 days per year.
3.3 PROGRAMMING PROPOSAL
Table 4 presents the proposed maintenance program for the 1K62 lathe, adapted to the specific conditions under which the assets operate, which differ from those in an industrial setting. In this program, certain activities do not need to be performed every 3510 hours but rather before and after the university’s teaching period, as this is when the lathe is used for research. This approach ensures better functioning of the equipment.
- Daily service: Displays tasks that need to be done each day.
- Review: Lists review of activities and their required hours.
- Small repair: Includes activities for minor repairs and the time allotted.
- Medium repair: Details of the intermediate level repair work.
- General repair: Presents the activities of a complete repair of the lathe.
To fully maintain the lathe, it is essential to completely disassemble it and replace any worn components in the clutches. All belts should be replaced as well. Additionally, the oil pump and filters need to be checked and either repaired or replaced if they are in poor condition, along with any faulty valves, pipes, fittings, cups, retainers, and seals. The oil reservoir must be thoroughly cleaned. Likewise, the coolant pump should be repaired or replaced, the filter changed, and any damaged pipes and seals must be replaced. The coolant reservoir also requires cleaning, and all oil tanks need to be painted on the inside. Afterward, reassemble all dismantled parts and mechanisms, ensuring they are cleaned, lubricated, and properly adjusted. Electrical parts should be inspected and repaired as necessary. Finally, test the lathe’s performance at all speeds and feet, paying close attention to detecting any unusual noises or excessive heating.
3.4 MATERIAL RESOURCES NEEDED FOR PPM
For small overhaul and repair: A slotted screwdriver, Allen wrench, preservation grease, a 4-inch brush, and a metal tweezer, all in a quantity of one.
For medium repair: A slotted screwdriver, Allen wrench, holding grease, two sandpapers, a 4-inch brush, and a metal tweezers, all in a quantity of one, except sandpaper, of which two units are required.
Other periodicity: A slotted screwdriver, an Allen wrench, 2 kg of bulk detergent, 8 liters of 46 circulation oil, storage grease, a 4-inch brush, 14 bearings and anticorrosive paint.
For the operator: two work overalls, masks, colorless glasses, two pairs of leather gloves, two pairs of work boots, a spatula, a caliper, and a caliper 150 mm high.
Table 4: Proposed actions for the MPP
Type of work | Instructions |
Daily service | Cleaning the machine |
Lubricate sliding surfaces | |
Observe the condition of the straps | |
Check that you gear them | |
Check coolant creep | |
Revision | Check cooling and lubrication systems |
Check the status of the guides | |
Clean, grease, and assemble disassembled parts | |
Evaluate the lathe in free running | |
Small repair | Cleaning, oiling, and mounting the disassembled mechanisms |
Evaluate the lathe in free running | |
Medium repair |
Disassemble all mechanisms |
Check the screw nut of the cross carriage | |
Remove any burs or scratches on all slides | |
Clean, grease and assemble all disassembled mechanisms | |
Draw up the list of defects and parts that will need to be replaced in the next planned repair. |
Source: Authors (2024).
4. FINAL CONSIDERATIONS
This work highlights the importance of having a preventive maintenance program to ensure that the 1K62 lathe is always available and running properly, helping to avoid unpleasant surprises. The new maintenance cycle we have proposed has proven effective in extending the lathe’s service life, allowing it to operate at its best capacity for a longer period. This focus on maintaining the 1K62 lathe not only benefits factories but also supports research in the Mechanical Engineering faculty, providing a practical example of how theories are applied in the real world and contributing to academic development. Finally, we suggest continuously reviewing and adapting the maintenance program according to operating conditions and feedback from technical staff to ensure its long-term effectiveness.
REFERENCES
MRA. Manual de mantenimiento y reparación de equipos industriales. Orbe, editor. La Habana 1980.
Abdelrahim EH, Vizvári B. Simultaneous scheduling of production and preventive maintenance on a single machine. Arabian Journal for Science and Engineering. 2017;42(7):2867-83. DOI 10.1007/s13369-016-2290-4
Costa RM, Sachetto JP. PLANEJAMENTO DA MANUTENÇÃO PREVENTIVA EM TORNO MECÂNICO ENGRENADO. Ciência & Tecnologia. 2023;15(1):e1519-e. https://doi.org/10.52138/citec.v15i1.329
Crespo MA, Moreu de León P, Sola Rosique A, Gómez Fernández JF. Criticality Analysis for Maintenance Purposes: A Study for Complex In‐service Engineering Assets. Quality and reliability engineering international. 2016;32(2):519-33. https://doi.org/10.1002/qre.1769
Díaz CA, Castillo Serpa AD, Villar Ledo L. Instrumento para evaluar el estado de la gestión de mantenimiento en plantas de bioproductos: Un caso de estudio. Ingeniare Revista chilena de ingeniería. 2017;25(2):306-13. http://dx.doi.org/10.4067/S0718-33052017000200306
Gunjan SB, Srinivasu D, Babu NR. Approach for determining the availability of machine tools based on skill level of operator and service personnel. Manufacturing Technology Today. 2023;22(2):67-72. DOI: 10.58368/MTT.22.2.2023.67-72
Jain M, Kumar P. Availability analysis of machining system with common cause failure, inspection and imperfect repair. Proceedings of the National Academy of Sciences, India Section A: Physical Sciences. 2021;91:451-60. https://doi.org/10.1007/s40010-020-00682-0
Marrero RA, Martínez-Pérez E, Vilalta-Alonso JA, García-Fenton V, Basile-Wilson M. La planificación del mantenimiento, su importancia en la gestión de los activos. Ingeniería Industrial. 2022;43:108-24. http://www.rii.cujae.edu.cu
Márquez AC, de León PM, Fernández JG, Márquez CP, González V. The maintenance management framework: A practical view to maintenance management. Safety, Reliability and Risk Analysis: CRC Press; 2008. p. 707-12. The maintenance management framework: A practical view to maintenance
Praedicow M, Apitzsch R, Richter A, Wunderlich T, Klimant P. Availability‐guaranteeing maintenance of series machine tools. Engineering Reports. 2022;4(7-8):e12456. https://doi.org/10.1002/eng2.12456
Patil RB, Mellal MA, Bewoor AK, Al-Dahidi S. Reliability, maintainability, and availability analysis of a computerized numerical control machine tool using Markov chains. Acta Polytechnica Hung. 2021;18(6):45-70. https://d1wqtxts1xzle7.cloudfront.net/78869721
Sevindik K. Parallel machine scheduling subject to machine availability constraints: Bilkent Universitesi (Turkey); 2006. https://www.proquest.com/openview/
Sosa JV, Quijada JL, Ontiveros MÁL, Montoya PP, Hernández AC. Mantenimiento industrial en máquinas herramientas por medio de AMFE. Revista Ingeniería Industrial. 2018;17(3). https://doi.org/10.22320/S07179103/2018.12
Stuchlý V, Poprocký R, Čuboňová N, Kuric I. Proposal of content maintenance of cnc machine using methods of reliability centered maintenance. Advances in Science and Technology Research Journal. 2018;12(3). DOI 10.12913/22998624/92094
Thoppil NM, Vasu V, Rao C. On the criticality analysis of computer numerical control lathe subsystems for predictive maintenance. Arabian Journal for Science and Engineering. 2020; 45:5259-71. https://doi.org/10.1007/s13369-020-04397-7
NOTE
The authors used Artificial Intelligence (Microsoft Office Copilot 2023) to correct the writing in English. However, all searches for content and classification of the quality of the articles were carried out in an authorial manner.
[1] Mechanical Engineer. ORCID: 0000-0002-3167-1072.
[2] Master in Mechanical Engineering. ORCID: https://orcid.org/0000-0003-4163-2656.
[3] PhD in Materials Science and Engineering. ORCID: https://orcid.org/0000-0003-0381-3851. Currículo Lattes: https://lattes.cnpq.br/8250462277774753.
[4] Master’s and PhD in Computational Modeling and Industrial Technology, Bachelor’s degree in Mathematics. ORCID: https://orcid.org/0000-0002-8193-5419. Currículo Lattes: http://lattes.cnpq.br/6235735011979354.
[5] PhD in Chemistry Master’s and Bachelor’s Degree in Chemistry. ORCID: 0000-0002-5739-7462. Currículo Lattes: http://lattes.cnpq.br/7216135300068165.
[6] PhD in Computational Modeling and Industrial Technology. ORCID: 0000-0001-7436-8818. Currículo Lattes: http://lattes.cnpq.br/2937471014216142.
[7] PhD . ORCID: https://orcid.org/0000-0002-9703-835X. Currículo Lattes: http://lattes.cnpq.br/7410531451699564.
[8] PhD . ORCID: https://orcid.org/0000-0002-3931-5953. Currículo Lattes: http://lattes.cnpq.br/4168723811261149.
Material received: November 27, 2024.
Material approved by peers: December 16, 2024.
Edited material approved by authors: January 15, 2024.